Using your infrared camera to extend equipment life
- weclfluke
- Jan 4, 2019
- 1 min read
Infrared cameras, also called thermal imagers, benefit preventive maintenance programs because they make preventive maintenance more efficient. With the range of sensitivity, resolution, and lenses available with today’s thermal imagers, you can get precise thermal detail from distances of a few inches to a few hundred feet. You can scan just about every component in your production system from a safe distance, while they’re operating. This can help you find issues before they blow up in your face—literally or figuratively. It can also help you lengthen maintenance intervals, while still extending equipment life. Some of the most common preventive maintenance applications for thermal imagers include:
Monitoring and measuring bearing temperatures and conditions in large motors and other rotating equipment
Identifying “hot spots” or “cold spots” in electronic equipment
Detecting leaks or determining fluid levels in sealed vessels and tanks
Locating faulty insulation in process pipes
Discovering faulty connections, loose contacts, or corrosion in high power electrical circuits
Locating overloaded circuit breakers in a power panel
Identifying fuses that are at or near their current rating capacity or that are improperly installed
Finding problems in electrical switch gear
Capturing process temperature readings
Monitoring transformer insulators and bushings in cramped underground vaults
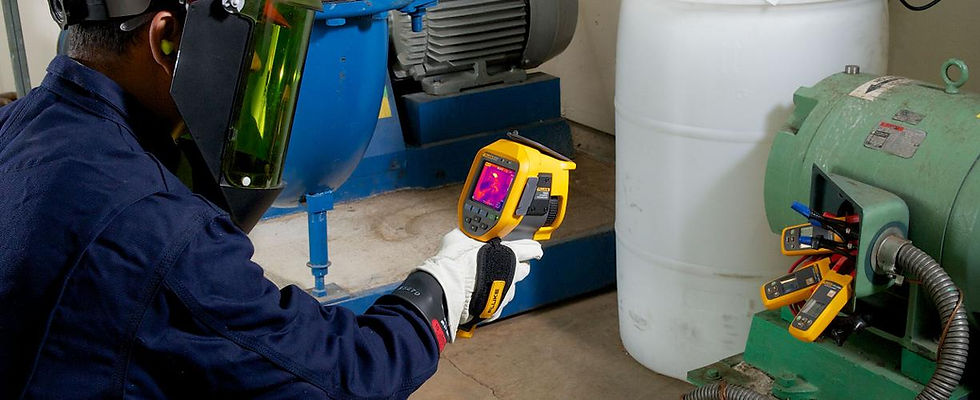
Original post: click HERE
Comments